My Thoughts on AI in the Waste Management Industry
- Ani Goswami
- Jul 9
- 7 min read
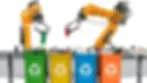
When I look at the mountains of material that pass through a modern materials-recovery facility (MRF), I cannot escape one thought: the twentieth-century tools we still rely on are no match for a twenty-first-century waste stream. Conveyor belts fly past at two metres a second, holding everything from yoghurt tubs to lithium batteries. Human eyes and hands were never designed for that pace or danger. Artificial intelligence (AI) changes the equation. It gives the industry the digital eyesight and split-second judgment it has lacked for decades.
Why AI Matters Right Now
AI turns an ordinary camera, vibration probe or GPS transponder into a sensor that understands what it sees. Trained computer-vision models can distinguish a milk bottle from a PET food tray, or a lithium-ion cell from a harmless AA, in a few milliseconds. Predictive algorithms then decide the best action—whether that is telling a robotic arm to pluck an item, warning a driver that a truck is overweight, or scheduling a baler service before the gearbox fails. The reward is twofold: higher recovery rates and lower risk.
The urgency is no longer academic. Australia has committed to recovering 80 per cent of all resources by 2030Â under its National Waste Policy Action Plan, an objective the federal environment minister has tied directly to circular-economy growth targets (dcceew.gov.au, theaustralian.com.au). At the same time, battery-related fires are spiralling. An industry survey conducted by Australian Council of Recycling published in June 2024Â estimates between 10,000 and 12,000 fires or heat events each year, adding more than $400 000 in average annual costs to an affected facility. Insurers are already signalling premium increases for operators that cannot demonstrate active detection and suppression. In short, the regulatory, financial and safety clocks are all ticking at once.
A Real-World Case Study: Portsmouth, Virginia
What does large-scale AI adoption look like in practice? A useful reference is the municipal-solid-waste (MSW) facility in Portsmouth, Virginia, run by Recycling & Disposal Solutions (RDS). In May 2024 the plant installed an AI-driven sortation line. The system uses high-resolution cameras and a catalogue of more than ten billion labelled images to guide delta robots that pick recyclables and organics directly out of black-bag waste. RDS now diverts about 60 per cent of material that previously went straight to landfill—an improvement achieved without a green-field rebuild. The lesson for the rest of the sector is simple: AI can bolt onto legacy infrastructure and start paying for itself within a single contract cycle.
Australia’s Digital Transformation Example
Closer to home, Cleanaway Waste Management is halfway through a $100 million four-year digital overhaul. The program combines an enterprise data lake with analytics that optimise routing, dynamic pricing and customer service. Fleet telemetry streams arrive every two minutes; transaction records now top 150 million entries a year. Management expects the analytics layer alone to add $5 million in EBIT in FY 2026 and to double that in FY 2027Â as smarter routing and differential pricing mature (itnews.com.au, news.microsoft.com). These numbers show that AI is no longer a pilot-plant curiosity but a line item that mainstream CFOs track.
Practical Use-Case Deep-Dives
1. Robotic Sortation
At the heart of AI-enabled recycling is robotic sortation. A line of vision-guided delta or articulated robots sits above the belt. Each robot is fed a real-time video stream. A convolutional neural network analyses every frame, labels the objects and sends precise X–Y coordinates and pick priorities to the robot controller. The best-known commercial systems, such as AMP Cortex and Oscorp Energy (obviously I am going to mention our name!), achieve pick rates of 80-150 items per minute—twice what an experienced human sorter can manage—and individual installations have logged peaks of 250 picks per minute with tandem units. Because the robots learn continuously, their accuracy now exceeds 95 per cent on positively sorted items, and they can recognise subtle visual cues such as brand logos or the dull finish of polypropylene versus PET. Over a shift, that speed advantage compounds into tonnage: a single robot can sort the same material that would otherwise require two to three human pickers, freeing people for safer, better-paid roles such as maintenance and quality auditing.
2. Hazard Detection and Fire Prevention
Lithium-ion cells hidden in toys, e-cigarettes or power-tool packs are today’s biggest operational hazard. AI models trained on infrared signatures and shape features flag suspect objects before they reach shredders or compactors. Some MRFs link the detection to an air-knife that shoots the battery sideways into a fire-resistant chute; others simply stop the belt and trigger a light tower so a supervisor can intervene. The return on investment is not abstract. The 10,000-plus fires each year cost millions in damaged equipment and insurance excesses (abc.net.au, acor.org.au). Facilities that adopt AI-based battery detection report immediate premium relief because they give underwriters quantifiable risk-reduction data.
3. Smart Bin Networks
Waste management begins long before a truck reaches the gate. In Sunderland, England, the city council has retrofitted more than 190 IoT fill-level and temperature sensors to public bins. Data flows into a smart-city platform that reroutes crews in real time, slashing unnecessary collections and fuel burn. Temperature alerts provide an early warning for potential fires in street bins—a growing concern as small lithium batteries proliferate. (sunderlandoursmartcity.com) The Sunderland trial illustrates how granular data, when stitched together with AI routing software, can shrink both carbon emissions and overtime budgets.
4. Route Optimisation
Traditional collection schedules treat every bin and suburb the same. AI-driven routing tools ingest historical fill data, real-time traffic and even weather forecasts to calculate the shortest loop that still hits bins just before they overflow. Cleanaway’s fleet analytics stack is an Australian proof point, but the same algorithms now come bundled in off-the-shelf platforms such as Geotab Waste or Sensoneo Route Planner. Fleet managers routinely see double-digit reductions in kilometres driven within the first quarter of deployment.
5. Predictive Maintenance
Conveyors, balers and optical sorters each have unique vibration and power-draw signatures when healthy. AI watches for deviations that foreshadow bearing wear or misalignment. Instead of waiting for a catastrophic failure that stops the line for 48 hours, maintenance crews swap a failing roller during a planned lunch break. Predictive maintenance platforms grew out of heavy manufacturing, so waste companies can adopt mature, proven tools rather than inventing new ones.
6. Commodity Pricing and Quality Audits
Because AI vision systems record every pick, they generate a census of material flows. Operators can certify bale purity down to half-percentage points and sell that transparency to mills hungry for high-grade feedstock. Dynamic pricing models then adjust gate fees or rebate structures in near-real time, using the cleaned data stream. Cleanaway’s CustomerConnect portal is an early example, but the same logic applies to any operator with a data warehouse.
7. Automated Regulatory Reporting
Manual sampling once forced plants to extrapolate from a few grab-samples. AI cameras create an auditable chain of evidence for every tonne processed. When state authorities ask for quarterly diversion reports, the numbers are already in the dashboard, complete with photo evidence. This shrinkage of compliance overhead becomes a competitive edge when tenders specify strict reporting cadence.
Benefits for Companies That Move First
Early adopters of AI in waste management realise gains on multiple fronts:
Higher recovery and revenue. RDS Portsmouth captures an extra 60 per cent of saleable commodities from municipal waste, turning what used to be a cost into cash.
Lower operating expense. Robots displace the most repetitive manual tasks; predictive routing cuts diesel bills; proactive maintenance avoids emergency call-outs. Cleanaway expects millions in incremental EBIT from analytics alone. (itnews.com.au)
Improved safety and insurance terms. Battery-detection systems directly address the fire hazards that drive insurance hikes. Facilities can document the risk-mitigation impact in actuarial terms, opening the door to lower excesses and broader cover.
Talent retention. Staff no longer stand in harm’s way sorting razor blades out of compost streams. Instead they supervise robots, analyse data or maintain electromechanical systems—roles that pay better and have clearer career paths.
Regulatory advantage. Transparent, real-time data aligns with the 80-per-cent recovery target and emerging product-stewardship reporting rules, positioning an AI-enabled plant as the safe bid in public tenders.
Risks of Sitting on the Sidelines
Delay is no longer neutral; it is an active decision to accept growing hazards and shrinking margins.
Insurance Drift. As underwriters incorporate fire surveys like ACOR’s, premiums for manual facilities will spike or cover will be withdrawn, leaving owners to self-insure catastrophic risk.
Tender Exclusion. Councils and consumer-goods firms increasingly demand traceable diversion data. Plants without AI instrumentation may find themselves locked out of long-term contracts.
Stranded Assets. Equipment bought today without AI integration points could need retrofits well before its mechanical lifespan ends, forcing double spending just to stay relevant.
Competitive Price Pressure. Operators who capture more saleable material can afford to reduce gate fees or offer better service-level agreements, squeezing late adopters in commodity and contract markets.
Regulatory Penalties. Failing to meet the 2030 resource-recovery targets risks fines, loss of licence extensions or forced upgrades under environmental-protection notices.
A Closing Call to Action
The waste industry often prides itself on caution—and rightly so, because we handle fire, chemicals and public health every day. Yet caution should not be mistaken for inertia. The Portsmouth and Cleanaway examples prove that AI is both mature and profitable. Every month we hesitate, a competitor installs another robot, an insurer recalculates risk, and a battery fire somewhere adds another black mark to the sector’s safety record.
The path forward is clear: start with a targeted pilot—maybe a single robotic sorter or a set of smart-bin sensors—collect the data, and let the numbers speak for themselves. From there, scale quickly, because the market, the regulators and the climate goals will not slow down to match a traditional capital-upgrade tempo.
AI is no longer the future of waste management; it is the present, and the longer we wait, the further we fall behind.